Step 1: Material Selection

The manufacturing process begins with selecting the right materials. Common fabrics used for baseball caps include cotton, polyester, wool, and synthetic blends. Each material is chosen based on the design, comfort, and durability requirements. At novae-apparel, we ensure that our materials are of the highest quality, suitable for different climates and purposes, and meet the needs of our clients worldwide.
Step 2: Cutting the Fabric
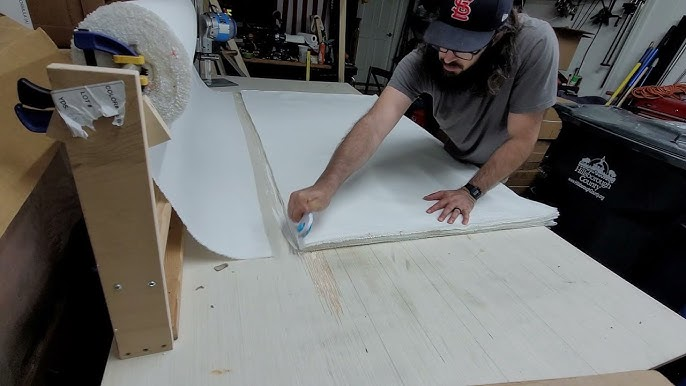
Once the fabric is selected, it is stacked in multiple layers and cut into specific pieces for the panels of the cap. This process is highly automated, using precision-cutting machines to ensure consistency in each piece while minimizing fabric waste.
Step 3: Sewing the Panels (Crown Construction)
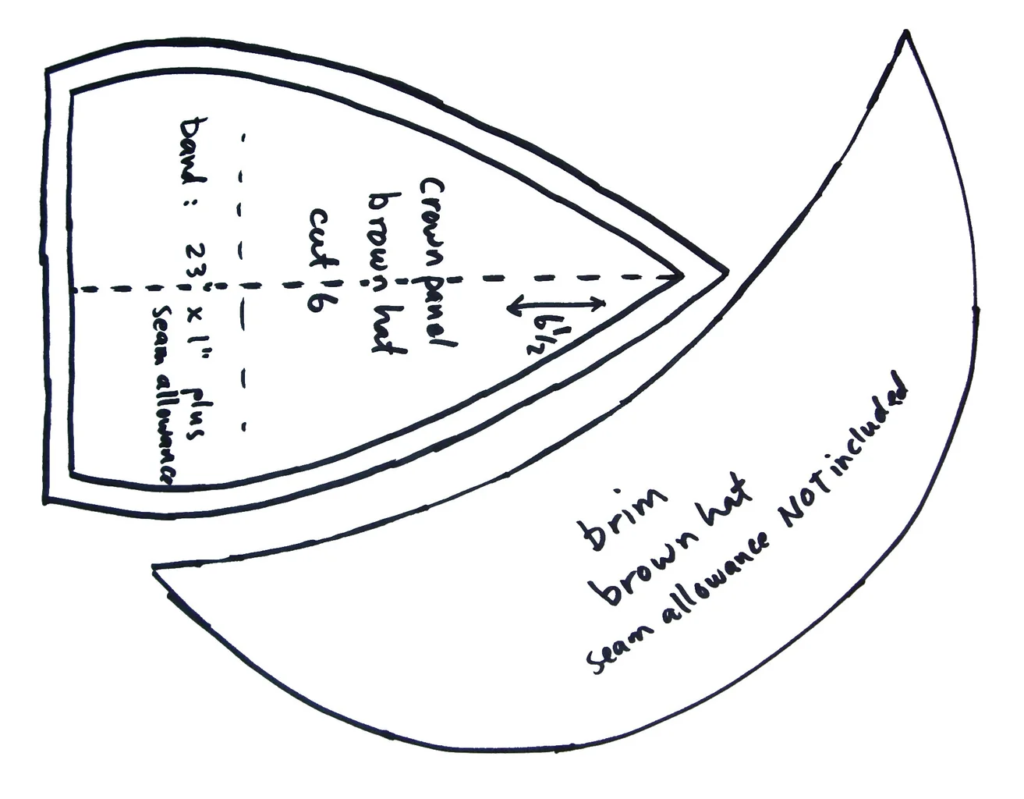
The next step is to assemble the panels that form the crown of the baseball cap. Each cap is made up of several panels: front, side, and back panels. These are stitched together, ensuring the shape and size of the crown fit well. For certain designs, such as trucker caps, a mesh fabric is used for the back panels to improve ventilation.
Step 4: Embroidery and Customization
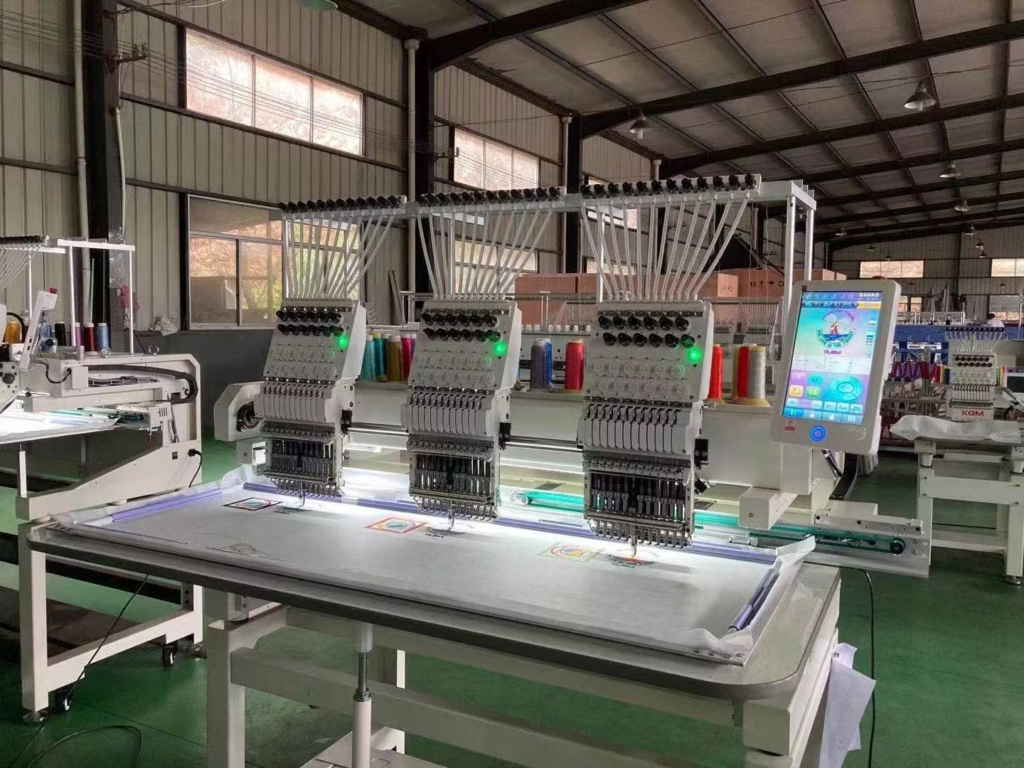
На сайте novae-apparel, we offer custom embroidery services where logos or designs are added directly onto the panels before they are fully assembled. Using advanced embroidery machines, we ensure that every logo or design is perfectly aligned, vivid in color, and durable enough to withstand wear and tear.
Step 5: Attaching the Eyelets

To enhance breathability, small eyelets are added near the top of the cap. These eyelets, either metal or sewn fabric, allow airflow and help keep the wearer cool. This step is crucial, especially for performance caps that need to be breathable for active users.
Step 6: Sewing the Visor
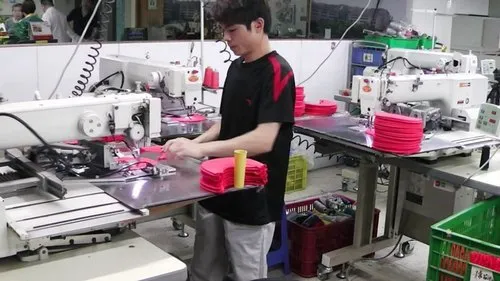
The visor, also known as the brim, is made separately. It consists of multiple fabric layers stitched together with a sturdy insert in between to maintain the shape. Depending on the cap design, the visor may be flat or curved. At novae-apparel, we ensure the visor is durable and maintains its shape over time.
Step 7: Attaching the Visor to the Crown
Once the visor is complete, it is attached to the front of the crown. This step requires precision to ensure the visor is securely stitched and perfectly aligned with the panels of the crown for a balanced and professional look.
Step 8: Adding the Sweatband
Inside the cap, a sweatband is sewn along the interior edge of the crown. The sweatband is designed to provide comfort and absorb sweat, making it especially useful for performance caps. novae-apparel uses moisture-wicking materials to enhance comfort, keeping wearers dry during extended use.
Step 9: Attaching the Closure
The closure system—whether it’s a snapback, buckle, velcro, or other adjustable methods—is attached at the back of the шапка. This allows the cap to fit various head sizes comfortably, making it versatile for different users. The closure is securely stitched to ensure durability.
Step 10: Quality Control and Packaging
The final step in our manufacturing process is a thorough quality control check. Every cap is inspected for stitching quality, alignment, logo placement, and overall construction. Only caps that pass this rigorous inspection are prepared for packaging. Once approved, the caps are neatly packaged and shipped to our customers, which include corporate buyers, brand owners, and distributors in the USA, Europe, and Canada.
Заключение
The manufacturing of baseball caps at novae-apparel combines advanced technology and expert craftsmanship to deliver high-quality products. Whether it’s choosing the best materials or ensuring every cap meets our strict quality standards, we take pride in every step of the process. With a monthly production capacity of 1.26 million pieces and a focus on customization, we cater to the needs of large corporate buyers and brand owners worldwide. For more information or to place an order, reach out to us at info@novae-apparel.com или посетите наш веб-сайт по адресу novae-apparel.com.